Lean methodology is the principle of eliminating waste and increasing productivity. It has been used in the manufacturing sector since the 1930s when the Toyota Car Plant introduced it to try and increase profits in a period of low demand for their products.Â
Today, lean is used by businesses in many different sectors, but it is particularly useful in the manufacturing sector, where costs can soon spiral if processes are not monitored. If the idea of lean manufacturing is something you’d like to learn more about, a manufacturing systems engineering masters from Kettering Online will be of interest. This type of qualification is very relevant in the manufacturing sector.
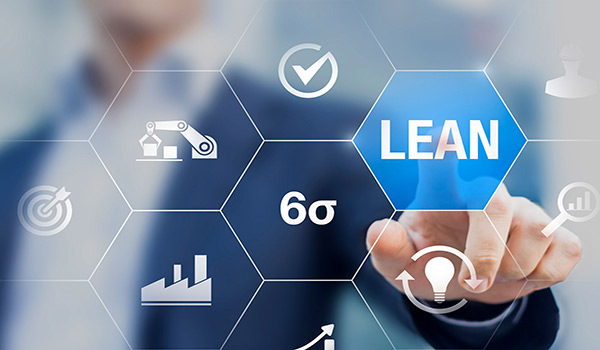
Read on to learn more about the pros and cons of lean manufacturing.
Table of Contents
The Advantages of Lean ManufacturingÂ
There are many advantages of implementing a lean approach in a manufacturing environment.Â
Eliminate Waste
Eliminating waste is a fundamental part of lean methodology. The goal is to remove waste in all its forms from every stage of the manufacturing process. This could be excess inventory, machinery not in use, too many workers on a shift, or obsolete inventory. By minimizing waste, such as excess inventory, you can reduce costs. For example, if you have too much inventory sitting on warehouse shelves, it is costing you money in storage fees. It’s also not cost-effective to pay workers to stand around chatting.
Reduced Lead Times
By implementing a more efficient manufacturing process, you can reduce product lead times. The faster you can bring a product to market, the better it is for the business. Fast lead times lead to better customer satisfaction and improved cash flow.Â
Improve Cash Flow
Shorter lead times will improve the company’s cash flow, as the sooner an order is delivered, the sooner the manufacturer will be paid. Since cash flow is king in all sectors, this advantage cannot be overstated enough.Â
Boost Worker Satisfaction
As stated, improved productivity boosts lead times, which in turn means happier customers. Long lead times can be detrimental to a manufacturer. Most customers in the digital age don’t want to wait for their products. This is a big problem if you supply products to a retailer, as they might have accepted orders and taken payment already. If you can’t deliver your products on time, the end customer is dissatisfied, and the retailer suffers the fallout. In a competitive marketplace, manufacturers can’t afford to upset their customers.Â
Gain a Competitive Advantage
The more efficient a manufacturer is at producing product and delivering it to customers, the more competitive they will be in the marketplace. If you operate in a highly competitive sector, such as the manufacture of consumer appliances, it is important to maximize your competitive advantages. By being more efficient and reducing waste, you can keep your operating costs low and your prices competitive, which is also advantageous.Â
Improved Customer Satisfaction
Customers will be a lot happier if their supplier can deliver a product on time and at a competitive price. Not meeting customer expectations can have a disastrous impact on a manufacturer’s reputation. Poor service will make it harder to secure new orders, and if problems persist, you could be out of business within a year.Â
The Disadvantages of Lean Manufacturing
While there are many benefits to implementing lean methodology in the manufacturing sector, it is important to be aware of the cons associated with lean manufacturing.Â
Low Morale Due to Increased Pressure on Workers
Part of being lean means squeezing more economy from workers on the production line. If managers are not careful, this can place too much pressure on workers to meet targets, and lead to low morale in the process. Be careful to monitor how the rigors of lean methodology are affecting your workforce. Make sure workers are fully educated on the advantages of lean before you introduce it to their working environment. Otherwise, you could see significant pushback from an aggrieved workforce.Â
Lower Margins for Error
The downside of honing your procedures in the pursuit of maximum efficiency is that it leaves you with little margin for error when something goes wrong. If a supplier issue affects your delivery of raw materials or there are too few workers available on a shift, this can cause bottlenecks in the production process. And without a ready supply of already manufactured inventory in stock, reduced production will impact your ability to fulfill client orders.Â
Missed Deliveries
The lack of flexibility in the lean manufacturing environment can cause a manufacturer to miss delivery deadlines. If you fail to meet shipment dates, customers won’t be happy, and repeated missed deadlines could lead to a loss of important contracts. Buyers won’t hesitate to look for suppliers that can meet their delivery targets.Â
No Room to Forecast for Changes
Lean manufacturing is very much focused on the here and now rather than what might happen in the future. This is good in some senses but bad in others. Being focused on the present makes it hard to look ahead into the future, and if a manufacturer doesn’t devote some time to implementing new strategies, research and development, and forecasting for future changes, it can lead to all kinds of issues.
All Employees Must Be on Board
It is very important to make sure all employees are on board with the ideology of lean manufacturing. Lean only works if everyone is willing to do their share of the work. The entire company must be overhauled to ensure all processes are as efficient as they can be. Workers may feel frustrated by the changes being implemented if they haven’t been properly explained to them. Be vigilant for signs of dissatisfaction and take the time to educate all employees about the advantages of switching to a lean environment.Â
Making the Switch to Lean
Lean is often more beneficial for small manufacturers that focus on producing small batches of niche products but producing products on a per-order basis also has advantages for producers of components.Â
Lean has many benefits, but you must carefully consider all the disadvantages before you overhaul your manufacturing processes.
Follow – https://viraldigimedia.com for More Updates